Ensuring compliance of CE-marked products
SATRA can assist with CE compliance for personal protective equipment (PPE) and ongoing supply chain compliance.
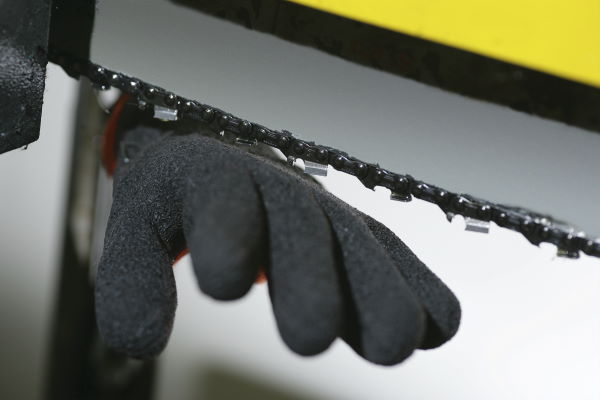
A key consideration for all types of personal protective equipment (PPE) is to ensure that the product has been appropriately CE marked, as this is a mandatory requirement for PPE products entering the European market. This not only covers evaluation of initial examples, but also bulk production.
It is difficult for European-sourcing PPE suppliers to fully control the supply chain. It is also simply not practical for many smaller organisations to confirm by themselves that every aspect of the products they are importing is satisfactory, as they lack both the infrastructure and the expertise. So, how can European suppliers (often not the manufacturer and frequently not even the importer), satisfy themselves that everything is in order and that they are meeting their obligations under the PPE Regulations? In addition, how do the EU type-examination certificate holders – whether they are manufacturers in their own right or resourcers, wholesalers and distributors – demonstrate compliance?
The answers to these questions depend on a number of factors, including the company’s position in the supply chain, and whether or not it is the type-examination certificate holder. As a leading European Notified Body, SATRA is well placed to help.
To start with, most types of PPE need to be assessed initially by a Notified Body such as SATRA, and a type-examination certificate issued before the CE mark can be applied (see box 1). Frequently, the manufacturer arranges this, but many resourcers, wholesalers and distributors also initiate the process to ensure they control the CE mark. In some cases, a certificate is supplemented or extended to include the details of the European supplier.
Box 1: Categories of PPE |
European legislation divides PPE into three categories, depending on the level of risk that the item of PPE is claimed to protect against. Each category requires a different level of involvement by a Notified Body:
|
The type-examination certificate holder then affixes the CE mark to the product and produces a ‘declaration of conformity’ – a document that includes details of the company, information on the product, a list of the European legislation and the standards the product complies with, and a legally-binding signature on behalf of the organisation. The onus is on the certificate holder to ensure that all supplied product is consistent with the type-approved model and continues to meet all the essential requirements of the PPE legislation.
What will the certification prove?
Many potential customers concentrate on obtaining copies of the type-examination certificate, believing that it will also demonstrate the bulk production will be compliant. In fact, the type-examination certificate merely confirms that the manufacturer has the capability to make the product correctly and can apply the CE mark to bulk production, providing it remains the same as the original type-approval samples. It does nothing to confirm the actual production, and purchasers should insist on being provided with an up-to-date test report on their actual batch.
It is relatively simple to document and demonstrate bulk product compliance through quality assurance systems, testing and inspection programmes if the type-examination certificate holder is the manufacturer with full control over the production. Whilst this can be done internally, use of a reputable third party like SATRA can provide independent confirmation to provide increased credibility.
Regardless of whether a resourcer, wholesaler or distributor holds the main type-examination certificate, or has a supplementary or extension certificate from the manufacturer, it is more difficult to demonstrate ongoing conformity. Sometimes the manufacturer will allow tests and audit facilities to be witnessed, and SATRA offers to do this on the customer’s behalf (thus saving on potential staff costs and time). Where it is not possible to visit factories, SATRA recommends testing a representative sample against the product specification. Using some form of sampling programme based on mathematical
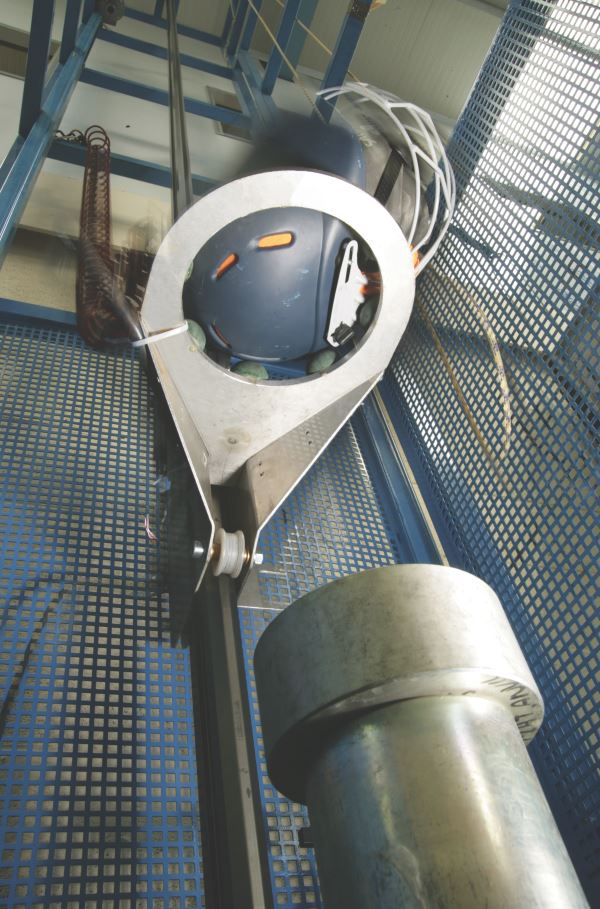
probability can help determine the amount of inspection and test required – for example, ISO 2859-1. SATRA has considerable experience of developing sampling plans and testing PPE and has the largest UKAS (United Kingdom Accreditation Service) testing scope in the UK to carry out the vast majority of the tests relating to PPE certifications. SATRA also offers a reputable test report based on the laboratory quality assurance standard ISO 17025 accredited by UKAS and is actively involved with all the European Notified Body decision-making and interpretation forums. SATRA customers in China can drop samples into our Dongguan facility and obtain test results in the same time – or frequently quicker – than local laboratories can provide.
In addition to our own comprehensive testing facilities, SATRA also runs an accredited laboratory programme for manufacturers’ in-house laboratories, which helps them demonstrate their commitment to product quality. SATRA oversees the quality system and confirms the technical staff competency to carry out an appropriate range of tests. In some cases, major brands insist on their suppliers having SATRA-accredited laboratories.
As a minimum, SATRA would recommend auditing of the manufacturer’s production facilities to ensure that product is being made in accordance with the technical file. Particular care should be taken to make sure all component and raw material purchases are from the companies listed in the master materials file, and that key safety critical features (for instance, toe cap impact and compression/midsole penetration insert resistance) are batch tested. These records should then tie in with shipment details to provide a direct link to the imported goods.

Checking colours of high-visibility material against European requirements
The best way to minimise defects is to work with manufacturers who believe in building good quality into the product in the first place. Whilst good contractual arrangements and working with reputable manufacturers can help, it is often prudent for resourcers, wholesalers and distributors to insist on becoming involved with aspects of quality assurance, inspection and testing of products. Using SATRA in this way need not be too costly or onerous, but can help provide reassurance that the products you are supplying are ‘fit for purpose’, safe and satisfy European legislation.
Enforcement and ‘due diligence’
PPE legislation is enforced throughout Europe by Member State enforcement bodies which have the powers to seize and destroy faulty goods. These enforcement authorities are active both at the port of entry and throughout the distribution chain, spot-checking products on sale. Once identified, unsafe or otherwise non-compliant products are notified to all EU Member States and a blanket ban is imposed.
If an unsafe product is found in the marketplace, the retail outlet that directly supplied the goods is potentially liable. The retailer – and, in many cases, the distributor or importer (often all three) – will be the subject of any investigation and subsequent enforcement action. If the manufacturer is also located in an area in which the enforcement authority has jurisdiction, it too could be investigated. Supplying substandard products can have disastrous consequences, ranging from loss of business, financial and reputation damage, through to substantial fines or even imprisonment if a serious safety offence has been committed. Retailers and distributors of consumer products need to be sure that what they are selling satisfies relevant legislation. In many cases, suppliers are required to provide the verification.
‘Due diligence’ defence
For most safety legislation that prohibits the placing of unsafe products on the market, it does not matter whether unsafe products are supplied deliberately or because an individual or company is unaware of the legal requirements. The fact that the law has been contravened is sufficient to allow a court to convict. However, one recognised defence to this type of ‘strict liability’ offence is ‘due diligence’, whereby the law may take into account the efforts made by businesses to comply with its demands in mitigation.
To use this defence, it must be shown that all reasonable precautions were addressed, and all steps taken to avoid committing the offence. If this can be done, the court can acquit the defendant. Whether or not a defence will be successful depends on the circumstances surrounding each case.
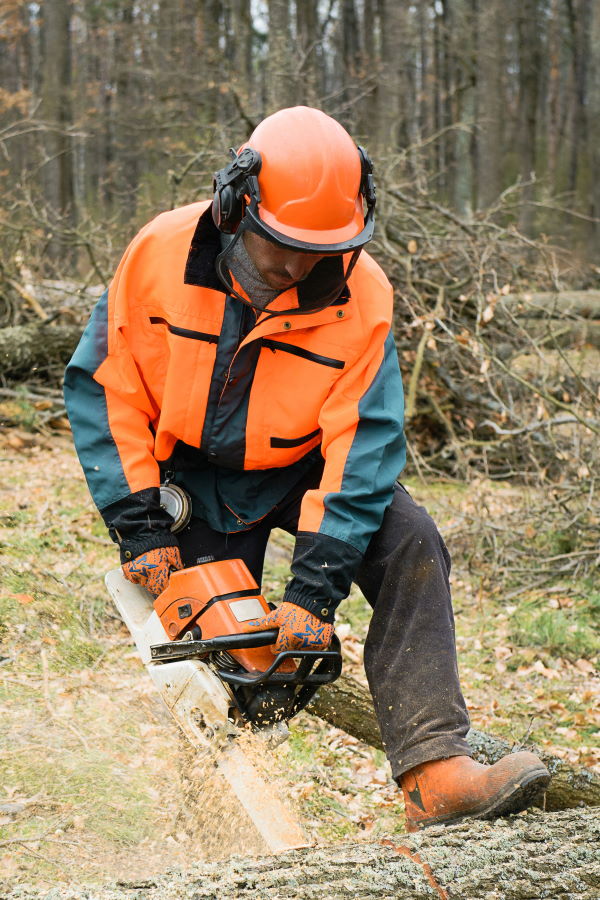
The size of the business, the amount of risk and the impact of failure associated with the product are some of the factors that the court will take into account to help to determine what are ‘all reasonable precautions’. What is considered reasonable for a small company may be considered inadequate for a larger one.
Traceability is essential
Effective procedures should be in place to show that the actual products being shipped are ‘quality assured’ and satisfy relevant legislation. Such procedures, coupled with an effective recall system if a problem does occur, will help with a ‘due diligence’ defence and may satisfy a court that the supplier ‘took all reasonable steps’ to prevent an inappropriate product from being placed on the market. This may prevent the supplier from being prosecuted. The measures described in this article go a long way to establishing this form of defence. However, it is essential to be able to identify the particular batches in question.
A number of recent problems with consumer goods have resulted in a total and public recall because the companies concerned could not identify or trace individual non-compliant batches. Therefore, it is essential when conducting ongoing production conformity checks, that results can be linked to each shipment made to the retailer.
In summary
Regardless of how it is carried out, most consumer protection legislation lays the responsibility for ensuring the product is safe with the person or organisation directly supplying the goods to the consumer. For strict liability safety offences, a robust ‘due diligence’ defence may prevent prosecution. However, it is far better to have processes and systems in place that minimise the possibility of an offence being committed in the first place. Western sourcing companies are more likely to work with manufacturers who can demonstrate a commitment to quality assurance and genuine interest in compliance with the PPE legislation for all their products – not just the ones used to obtain the initial type-examination certificate.
Further information on SATRA’s PPE certification and testing services is available at www.satra.nz/
How can we help?
15 PER CENT DISCOUNT ON FIRST SATRA TEST – please click here.
Please email [email protected] if you require help with SATRA high-visibility tape testing or certification.
Technical links
Back protection for winter sports
Determining the useful life of PPE
Helping retailers to understand their REACH obligations
High-speed particle testing of eyewear
High visibility on the railways
High-visibility retro-reflective materials
ISO 13997 cut resistance testing
Karabiners and fall protection connectors
Laboratory accreditation for PPE producers