Automotive materials and components testing
Automotive Original Equipment Manufacturers (OEMs) demand the highest quality components throughout the supply chain. Every automotive material and component must undergo rigorous testing and meet the highest industry and legal requirements. SATRA assists manufacturers and suppliers with independent assured testing services against a wide range of OEM testing specifications, national (BS, ASTM, DIN, JASO) and international (ISO, EN, SAE) standards. SATRA’s testing services are accredited to ISO 17025.
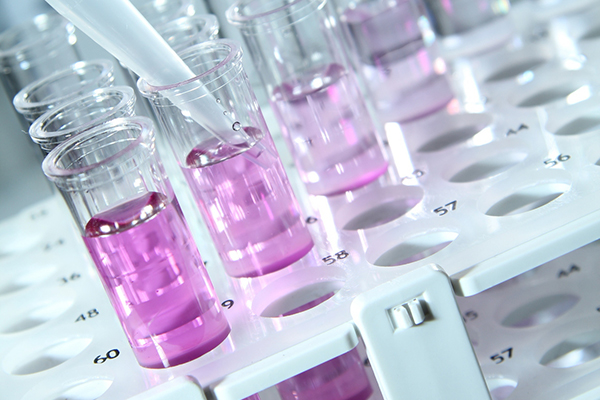
Chemical
Each OEM has detailed material specifications that aim to control the use of undesirable constituents that may have an impact on the environment or health. SATRA has its own chemical analysis laboratory to assess materials used in automotive interiors for the presence of restricted or harmful substances.
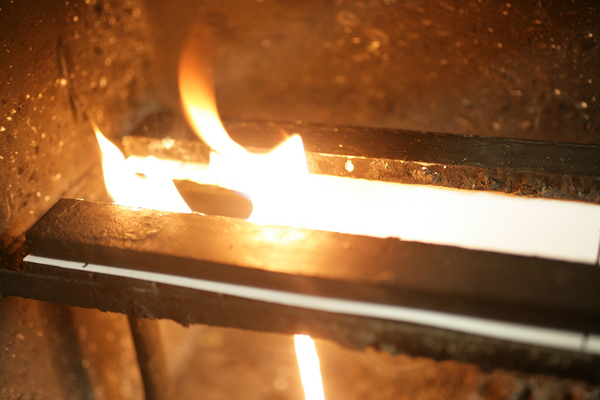
Flammability
Motor vehicles contain components that burn if subjected to a large enough ignition source. These include seat upholstery, headlining, trim panels and floor coverings. SATRA can conduct a range of flammability tests including FMVSS 302 and ISO 3795.
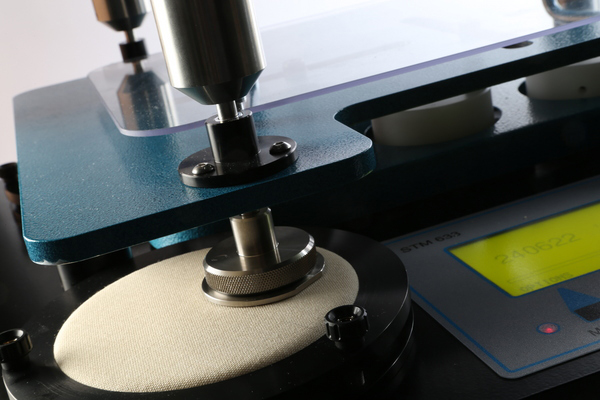
Abrasion and scratch resistance
Automotive materials experience mild abrasive actions from users entering the vehicle and being seated while driving or travelling. SATRA has a range of tests including Martindale and Taber abrasion and can advise on the correct method and specification depending on the end use. Plastic components may be tested for scratch resistance using a metallic scribe which is applied to the test surface with an increasing force. Painted plastics can be assessed by carrying out a cross-hatch test where the finish is scoured in a grid pattern and adhesive tape used to assess the ease at which the painted layer is removed.
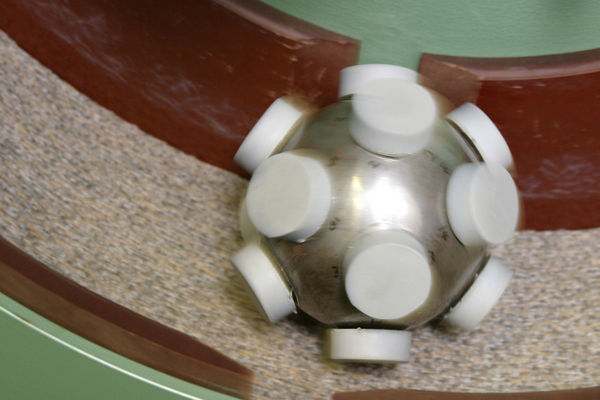
Wear resistance
Carpets, floor coverings and low level trims used in automotive vehicles need to possess a good degree of resilience to prevent the appearance of premature signs of wear. The wear properties of these components can be assessed through abrasion testing which may be carried out with the Tabor method or a drum abrasion method using a hexapod that has six polyurethane studs that randomly roll across the carpet surface. Tested carpets are assessed visually for damage, for example tuft pull out, snagging and laddering or, alternatively, by calculating mass loss.
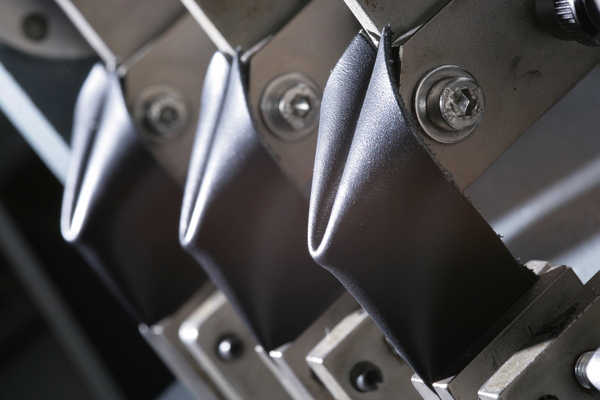
Flexing endurance
The degree that leather and coated fabrics will flex will depend on the end use. For example, leather used as a door panel is unlikely to experience significant flexing, whereas upholstery leather will flex every time the driver and passengers are seated. The traditional way of assessing flexing endurance is by carrying out a Bally flex test, though some OEMs include Shildknecht (W flex) or De Mattia flexing tests as an alternative. Leather is usually visually assessed for cracking of the grain and delamination of finishes caused by the flexing procedure. Some PU materials are prone to breakdown caused by hydrolytic attack from water molecules which can cause severe deterioration of the material’s coated layer. To investigate a material’s resistance to this type of break down flexing tests can be carried out after conditioning samples at high temperatures and humidity conditions. PU materials are also known to perform poorly under cold temperature conditions and SATRA is able to carry out cold crack resistance testing.
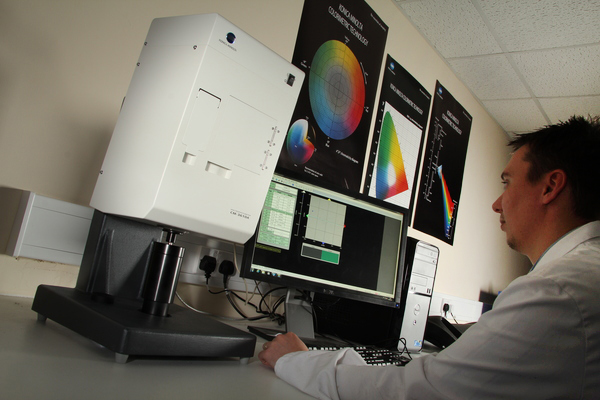
Colour
The materials used for automotive upholstery and trim need to offer sufficient resistance to soiling, staining and colour change. Automotive interiors may be exposed to direct sunlight for long periods of time and appropriate laboratory testing can investigate the likelihood of materials fading due to poor light fastness. SATRA has the capability to carry out assessments using a xenon lamp light fastness tester across a range of different methods. It is often the requirement of a test method to measure the degree of colour change or staining caused by the test procedure. The assessment could be a description of the damage seen, as a subjective Grey Scale Rating or, alternatively, by the use of a digital colorimeter which can express viewed colour as a L*a*b* value, which is ideal for measuring small degrees of colour change. SATRA is also able to carry out assessments of rub fastness and colour transfer tests.
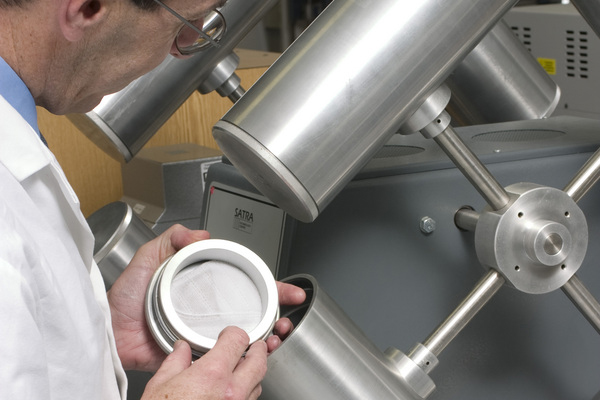
Staining and cleanability
Automotive upholstery and trim need to offer acceptable levels of resistance to soiling, staining and colour change. Once soiled, some components may be difficult to effectively clean in situ. Carpets are particularly at risk of staining. At SATRA we can assess the soiling resistance and cleanability of materials and test their resistance to a range of cleaning products likely to encountered during normal use. SATRA is also able to carry out assessments of rub fastness and colour transfer tests.
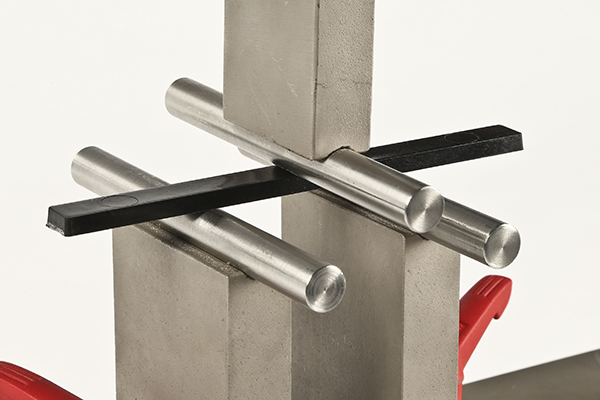
Strength
The results obtained from conducting strength tests on materials including leather, textile and coated fabric, give a good indication of the quality of the material and its suitability for its intended end use. Tensile and tear strength tests are useful as general quality assessments and seam strength tests are applicable to materials used in specific applications and vehicle locations, for example threads used to sew upholstery. SATRA is able to offer a comprehensive range of assessments to examine material strength as new and after heat and humidity ageing. Plastic materials may be formed into plaques and tested for breaking strength as a general quality assessment. Once the plastic has been formed into vehicle components such as whole instrument panels, larger scale strength and deformation tests may be a more appropriate method of assessment.
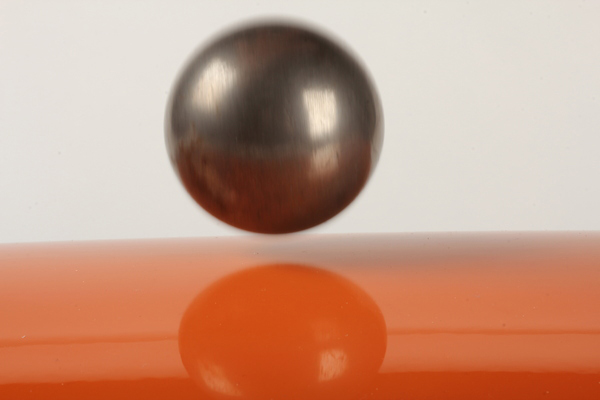
Impact resistance
Moulded plastic plaques can be tested for impact resistance using various methods including Izod and Charpy methods. These tests are useful for comparing the relative impact resistance of different materials. Formed plastic components may be at risk of deformation or damage from accidental impacts or compression during use. SATRA can carry out standard impact testing by dropping a spherical ball onto moulded components or compression and deformation tests using a tensile tester on vulnerable locations of components.
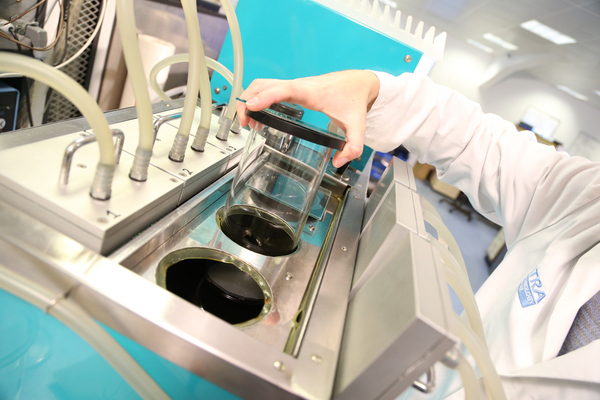
Resistance to fogging
Automotive interior components may contain semi-volatile constituents such as oils which could evaporate into the atmosphere within the vehicle’s cabin. In a gaseous state these constituents come into contact with the cooler glass of the automotive windscreen where they may condense and cause the formation of a clear film, droplets or crystals on the surface of the glass. A build-up of these condensed deposits may cause scattering of the light passing through the windscreen and affect driver visibility. Laboratory testing can assess the degree of fogging a material is likely to produce. SATRA is able to carry out both gravimetric and photometric methods of analysis.
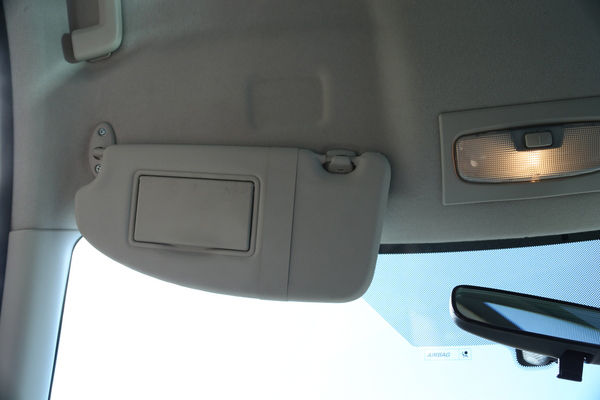
Environmental impact on interiors
Automotive interiors need to be able to withstand extreme changes in temperature. Interior units may be assembled from a number of individual components and should perform without dimensional change, bending or warping. Units that comprise several materials may be at a greater risk of damage if the separate materials react to the changes in temperature in different ways. In addition, any adhesive used to bond materials may also be adversely affected. SATRA possesses heat and humidity controlled cyclic chambers capable of replicating sudden and significant temperature changes between -40°C and 200°C and large enough to accommodate whole instrument panels, consoles and dashboards. Units can also be assessed for operational loading strengths, such as assessing the load required to operate a glove box latch, as well as additional endurance tests to ensure operating features last the lifetime of the vehicle.
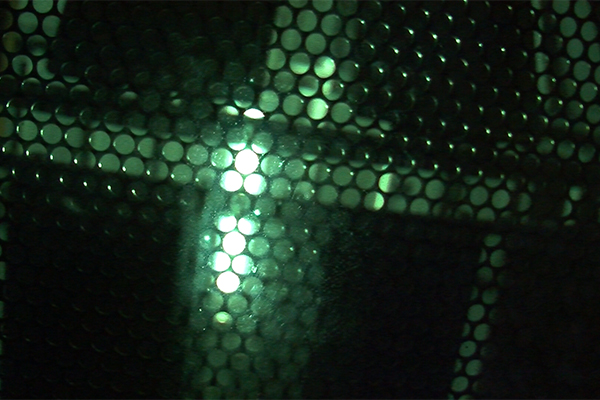
Weathering
Exterior materials and components are not only exposed to light but also adverse weather conditions. The aim of weathering testing is to simulate the effects of rain wetting a material, followed by the sun’s radiation drying the material. The exposure cycle (including, if necessary, periods of light exposure alternating with darkness) will be dependent upon the specific method employed as, for example, outlined in SAE J1960, SAE J2527 and Nissan Engineering Standard (NES) M0135. SATRA has two weatherometer chambers.
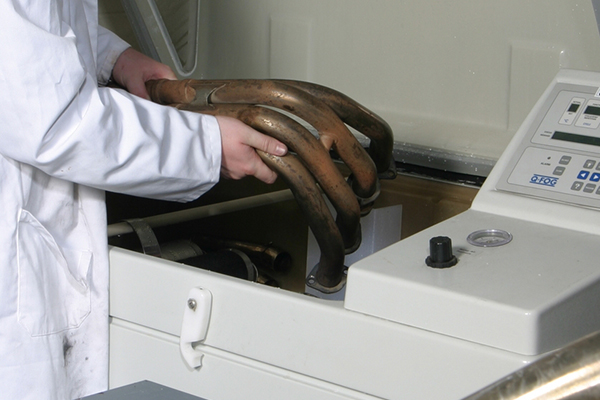
Corrosion
Many automotive components, particularly metal, are at risk of salt corrosion. Degradation will occur from either electrochemical or chemical processes with different materials or protective coatings reacting at varying rates. Corrosion problems can lead to costly repairs and cause considerable brand damage. By providing results in a relatively short time, accelerated ageing corrosion tests can help engineers to select material types and refine designs to minimise susceptibility to the effects of corrosion. Corrosion tests typically involve the spraying of a salt solution in a testing chamber, either at 35°C or 50°C. SATRA can undertake such testing where required.
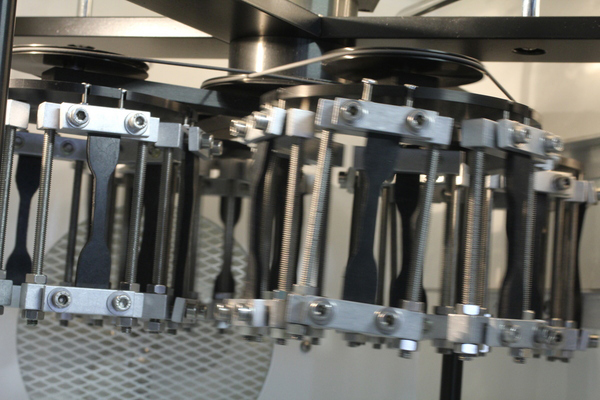
Ozone
It is essential that components used in and around the engine compartment have an adequate resistance to ozone. Ozone is typically generated under the bonnet by electrical equipment and can attack and rapidly degrade certain materials, particularly components made of rubber, for example brake and fuel hoses and seals. SATRA has its own ozone exposure chamber capable of exposing samples to a controlled concentration of ozone. Examination of the exposed samples under magnification can reveal signs of cracking. SATRA is able to test to various international standards including ISO 1431 and ASTM D1149.
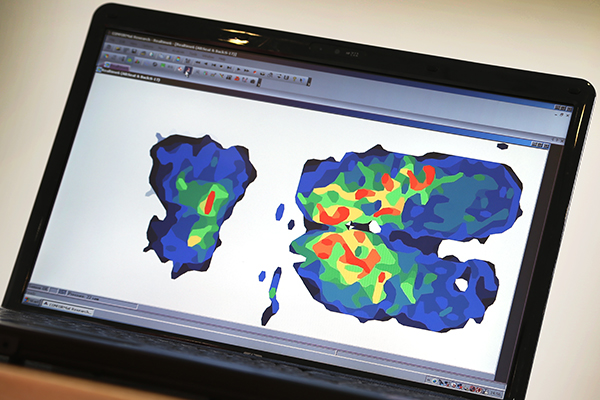
Bespoke research and testing
SATRA not only carries out testing in accordance with recognised specifications and test methods, but also works with customers to develop bespoke research and testing programmes for materials or properties where there is no recognised procedure or method. Examples of projects include: analysis of welded seam integrity for vehicle seating before and after fatigue testing; air bag chute hinge attachment strength; assessment of high frequency welding strength on plastic components; pressure mapping of seating systems; development of a test method for examining flexing resistance of vinyl side panels for vehicle seating.